In my career, I’ve encountered several non-traditional ways to build a home, from stacking hay bales to rolling out plastic tubes to using 3D-printed concrete. They’ve been fun to talk about but never made the slightest dent in the industry. The labor-intensive process of “stick-building” houses onsite remains the norm.
That failure doesn’t mean we should stop trying, however, so let’s look at an intriguing idea being developed at the University of Maine.
The school’s Advanced Structures and Composite Center in Orono recently wrapped up the first year’s outdoor test of BioHome2, a 3D-printed house made entirely of wood fibers impregnated with resin and squeezed out of an industrial-sized printer head. And I mean entirely: They even used it to print the roof of the small but serviceable (600 square feet) one-bedroom home.
“We wanted to see how it does through a Maine winter. We’ve done a lot of testing in lab, weathering tests and material tests, but there’s nothing like putting it out there,” said Habib Dagher, executive director of the center.
They were worried about it collapsing under snow load or blowing away in a Nor’Easter, of course, but also more subtle potential issues. “One of our big concerns was how it would expand and contract under different temperatures. We had some drywall attached – would it stay? Would it shift by differential expansion? But we didn’t see that,” said Dagher.
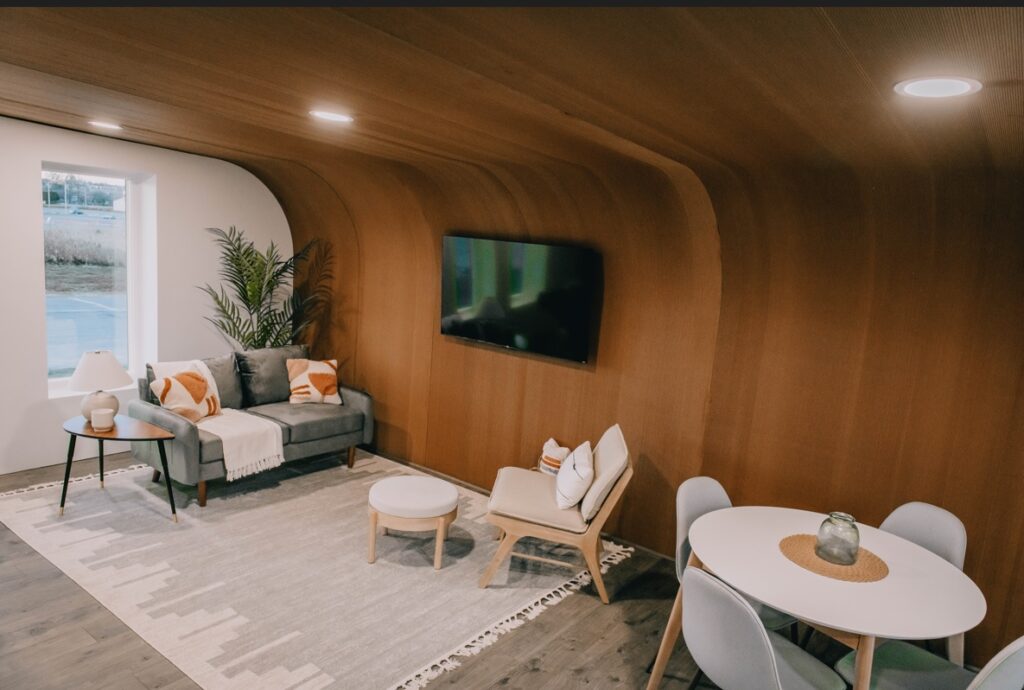
The basic idea behind BioHome is as old as the first mobile home: It’s cheaper and often better to build a house in a controlled indoor facility and then move it to the final location, instead of gathering materials at each housing site and getting a crew to assemble them in the wind and rain and snow. That sounds obvious but such modular construction has never quite caught on for many reasons, from the low-rent reputation of “trailer parks” to the width limitations of moving structures along the highway.
BioHome adds two potential advantages to modular construction. One is 3D-printing, which reduces the number of people needed to build a house. That’s even more of an advantage in the post-pandemic labor market, where trained construction workers are worth their weight in Snap-On tools. Printing also provides more flexibility in design, one reason the BioHome with its sloping corners looks so unusual.
The other potential benefit is its unusual material. The lab has created a mix of wood fiber and “bio-resin” in pellet form to feed its printers. The result is wood – you can cut it or drill holes in it, hang pictures or drywall on it, and paint it, Dagher said – but it’s wood created in large forms, very different than the balloon structure of most homes.
The raw material is valuable from the point of view of Maine (and New Hampshire) since it uses waste wood, the forestry and sawmill byproduct that once fed New England’s massive paper mills before that business moved away. Creating a new market for waste wood would be a big benefit for New England’s forest industry.
All this is fine and dandy but BioHome will just be another in a long list of “futuristic” houses that never move past novelty status if it can’t be built in large numbers at reasonable cost. That’s the next stage at Orono.
The Advanced Structures and Composite Center will break ground this summer on an expansion they’re calling the Green Engineering and Materials (GEM) Factory of the Future, the next step in BioHome development.
“Cost is a function of how fast you can print it,” said Dagher. Currently, the extruder head can print 120 pounds an hour, moved around by an overhead gantry crane. The next generation should go to 500 pounds an hour, he said. The one-bedroom home requires around 40,000 pounds of material so if they get a couple of the new printers going in the new factory they could in theory produce a home every 2 days with an estimated material cost of $40,000, although that doesn’t include moving, installation and what is often the biggest cost, land.
The lab is working on a plan to print nine homes with the next generation of their BioHome3D technology and put them in Bangor to provide housing for individuals experiencing or at risk of homelessness. And importantly, they’re working on standards and training so that local building inspectors, often a stumbling block for unusual housing designs, can be confident about the safety of these weird objects.
All this reflects the fact that new technology is just the start of making a difference in something as sweeping and important as our housing.
“We don’t anticipate that this would be the only way to make houses. It’s just another tool, another solution, that can add to the housing stock,” said Dagher.
And we all know the nation’s housing crisis needs all the tools and solutions it can get. Even if they come oozing out of a gigantic printer.
Nice looking house, I’d live in it.
Go USM!!
How does the house’s energy efficiency stack up? What is the R value of the walls and roof?
I like it. That looks like Ikea furniture inside ; they should consider a partnership, maybe. I wonder how easy/difficult it might prove to get the slab set with all the plumbing and electric hook-ups in place so it all lines up correctly, “plug and play,” when the house arrives.